The ACT UK project findings
The ACT UK project concluded in 2025. But what were the project findings?
The Autosort for Circular Textiles Demonstrator (ACT UK) project aimed to produce a blueprint for a fully integrated, automated sorting and pre-processing demonstrator for waste textiles. Spearheaded by the UKFT and supported by a cooperative of industry leaders, including Shred Station, the £4 million, two-year project reached its conclusion in early 2025. Here’s what the project achieved.
The goals of the project
Every year, the UK generates an enormous amount of textile waste. Of this waste, around 744,000 tonnes are textiles that are no longer wearable. The majority of these non-rewearable textiles (NRTs) are sent to landfill (61,000 tonnes), incineration (469,000 tonnes), or are exported overseas to regions with low labour costs (158,000 tonnes).
At present, the nation’s textile waste processes are unsustainable, both financially and environmentally. The ACT UK business case report, published by WRAP, revealed that the estimated cost of sorting just under half (363,000 tonnes) of the UK’s NRTs alone, as it presently operates, will cost the textile sector £77 million annually by 2035. This excludes collection costs. With collection costs included, this figure already sits at £88m per year. NRTs also put a huge financial strain on charities, which must often pay to dispose of them. For some charities, this burden can come with a hefty price tag, exceeding tens of thousands of pounds each year.
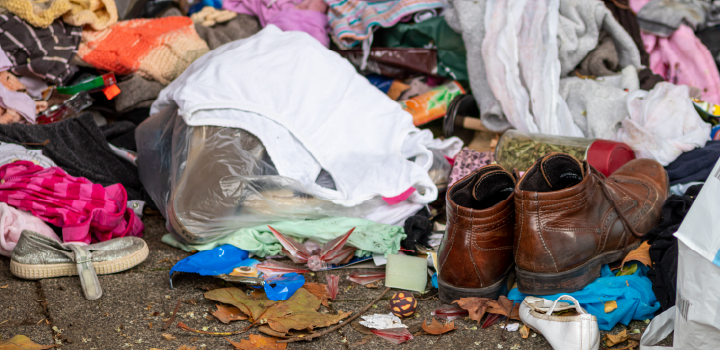
Sustainability
Sustainability-wise, the textiles industry overall has a lot of room for improvement. It’s estimated that 8-10% of global greenhouse gas emissions come from the fashion and textiles industry. Textile production is also thought to be responsible for c.20% of global clean water pollution from dyeing and finishing products. A single laundry load of polyester products can release up to 700,000 microplastic fibres into the food chain, and only 1% of used textiles are recycled back into textile products. WRAP’s report states that:
“This huge disparity between the vast amount of used textiles being discarded, and the proportionally tiny amount being turned back into textile products, demonstrates both the scale of the issue with the current system, and the huge potential for a future system that works for all parts of the value chain within it”.
The ACT UK project goals were, in simple terms, to identify whether a better, more economical, and more sustainable solution was feasible. The ACT UK project aimed to develop solutions and design the infrastructure to manage the UK’s unwanted and unusable clothing and textiles. By optimising used textile collections, gathering insights into people’s knowledge and behaviours around unwanted textiles, and creating the blueprints for the world’s first automatic sorting and pre-processing plant for waste textiles, the ACT UK project established the business case and feasibility of a network of automated sorting facilities across the UK. This network could significantly reduce disposal costs and improve recycling rates for waste textiles.
Project achievements and findings
The project, which spanned over two years, provided some key insights into the feasibility of automatic sorting and pre-processing plants and, fundamentally, the public’s appetite and ability to segregate NRTs from other textiles. You can read the full project report here.
The ACT UK Project did identify holes in the UK’s current handling of waste textiles… However, it also identified solutions.
Some of these are detailed below.
Sorting textiles that can be re-worn or reused from those that can’t
Separating re-wearable textiles and non-rewearable textiles currently involves human input, and it’s quite subjective. What one member of the public would consider suitable for re-use, another may not.
The ACT UK – Transitioning to a UK Circular Textiles Ecosystem report reveals that citizens who took part in the ACT UK’s pre-sorting trials did not successfully separate rewearables and non-rewearables. At present, this sortation is done manually by skilled and experienced professionals, which is expensive and time-consuming. The project proposes that AI could be used to support the sector in streamlining this labour-intensive process.
Automatic sorting for NRTs at scale
To increase the volume of NRTs that are recycled, The ACT Project put forward a business case for a network of 14 advanced textile sorting and preprocessing (ATSP) facilities across the UK. It compared 6 automated sorting technology providers, each of which uses near-infrared spectroscopy to sort materials. The project’s blueprint for ATSPs could mean each plant processes between 2.5 and 12.5 tonnes of textiles per hour. This network of ATSPs could prevent over 350,000 tonnes of textiles from being lost to landfill and incineration. So, why isn’t this already happening?
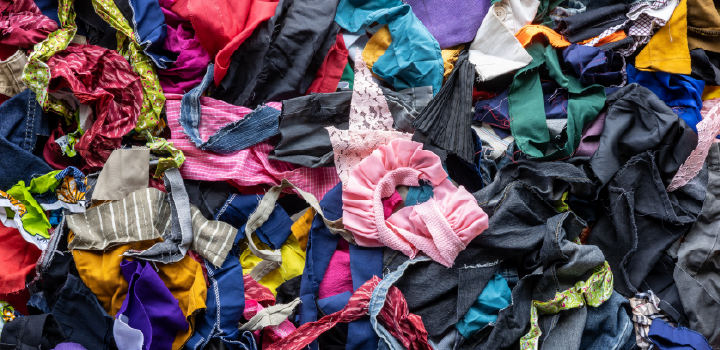
The true cost of clothing waste
The textile sorting industry, as it currently operates in the UK, is a professional and specialised sector. However, it is haemorrhaging money.
Previously, the cost of sorting NRTs was subsidised by the sale of textiles that were rewearable. It was also propped up by international exports, where countries like Pakistan and the UAE were happy to receive NRTs for their own markets.
Now, with an increase in fast fashion, the resale value of textiles is low due to oversupply, cheaper, and lower-quality fabrics. Operational costs are also higher, as is competition for overseas exports, leading to oversupply. There are also growing public concerns surrounding clothing exports, a lack of government-backed policies for used textiles, no capital investment, and no end producer responsibility on manufacturers, as we see with things like electronic waste.
It is estimated that the current process of sorting a single tonne of NRTs is creating an average loss of £426. Without intervention, large parts of the sector could be at risk of collapse.
What would a collapse mean?
- Charities, local authorities and consumers would have to pay the price of industry inaction. The estimated increased cost to local authorities through gate fees alone is £64m, which could become £200m by 2035.
- The UK’s carbon emissions could rise by 2.5m tonnes CO2e each year as more textiles are landfilled or burnt.
- The implementation of the UK Emissions Trading Scheme in 2028 will mean that local authorities will be charged a levy for textiles disposed of in general waste streams, including those destined for incineration and Energy from Waste. These increased costs to local authorities could be passed on to citizens through taxes. Diverting textiles from general waste will therefore require reform, and the public will need to get better at sorting textile waste. This could require even more resources, campaigns, educational literature, and public funds.
Is there a potential future for ATSPs?
The ACT UK project business case report states that:
“Investment in ATSPs as a route for taking NRT will present a cost-effective route for councils and local authorities who are already financially stretched. These increased costs to local authorities could also get passed onto citizens via taxes, meaning that behaviour change to divert textiles from residual waste will become increasingly important to avoid economic issues.”
The project consortium modelled the impact of running 14 ATSPs across the UK. It found that these plants would cost 51% less than keeping to the current system. While this would still mean starting at a loss, there would be an opportunity to break even or become profitable further down the line if the government were to introduce end producer responsibility for textile manufacturers. Each sorting facility could also create between 18 and 53 full-time job opportunities. If adopted across Europe, ATSPs could create over 100,000 jobs.
The WRAP report continues:
“If the circular textiles ecosystem is to become economically successful, it will be vital for ‘waste’ textiles to be seen instead as a reusable resource and to increase the value of the ‘low value’ half. This perception shift is not only relevant in textiles but is critical to all aspects of a future circular economy. However, this will not be possible within the current linear system, and systems change and adaptation is needed”
“It must be recognised that no single company alone can transform the entire supply chain and bring a new one to life. New types of commitment and long-term collaborations are needed between brands and retailers, collectors and sorters, ATSPs, recyclers and the rest of the value chain to scale the next generation of the textiles system”.
It’s not yet clear if a network of ATSPs will ever be introduced across the UK. However, what this project has made clear is that reform is urgently needed to ensure that the textile sorting industry continues to operate. Even without ATSPs considered, if this industry fails, there are huge environmental impacts.
Sources:
WRAP. (2025) ‘Advanced Textile Sorting and Pre-processing Facilities: The Business Case’. Available at: https://www.wrap.ngo/resources/report/act-uk-business-case-advanced-textile-sorting-and-pre-processing-facilities
WRAP. (2025) ‘Transitioning to a UK Circular Textiles Ecosystem’. Available at: https://www.wrap.ngo/resources/report/act-uk-transitioning-uk-circular-textiles-ecosystem-report
Sign up for our newsletter to receive alerts about new blog articles, data protection advice, and Shred Station news.